- +91 8123115793
- info@kankengineers.com
- Banashankari 6th Stage, Bangalore 560062
Pre Engineered Building
Pre-engineered Metal Buildings (PEB)

Pre-Engineered Building is a manufacturing concept replacing traditional or conventional manufacturing. PEBs is seen as a breakthrough in the construction industry, resulting in less construction time, cost-effectiveness, high quality, low maintenance, consistent span. Pre-engineered buildings meet one of industry’s most critical criteria that is wide, column-free areas.
Kanaje Engineer is a global enterprise, which specializes in providing solutions for Pre-engineered Buildings and Structural Steel.
In structural engineering, a pre-engineered building (PEB) is designed by a PEB supplier or PEB manufacturer with a single design to be fabricated using various materials and methods to satisfy a wide range of structural and aesthetic design requirements

Comparison Between Pre Engineer and Steel building
Properties
Pre Engineered Steel Building
Steel builing
Structural Weight | Pre-engineered buildings are on the average 30% lighter because of the efficient use of steel. | Primary steel members are selected hot rolled “T” sections. Which are, in many segments of the members heavier than what is actually required by design. |
Design | Quick and efficient design since PEB’s are mainly formed by standard sections and connections design, time is significantly reduced. | Each conventional steel structure is designed from scratch with fewer design aids available to the engineer. |
Construction Period | Average 6 to 8 weeks | Average 20 to 26 weeks |
Foundation | Simple design, easy to construct and light weight. | Extensive, heavy foundation required. |
Erection and Simplicity | Since the connection of compounds is standard the learning curve of erection for each subsequent project is faster. | The connections are normally complicated and differ from project to project resulting tin increasing the time for erection of the buildings. |
Erection Time and Cost | The erection process is faster and much easier with very less requirement for equipment | Typically, conventional steel buildings are 20% more expensive than PEB in most of the cases, the erection costs and time are not estimated accurately. |
Seismic Reistance | The low weight flexible frames offer higher resistance to seismic forces. | Rigid heavy frames do not perform well in seismic zones. |
Over all Cost | Price per square meter may be as low as by 30 % than the conventional building. | Higher price per square meter. |
Architecture | Outstanding architectural design can be achieved at low cost using standard architectural details and interfaces. | Special architectural design and features must be developed for each project which often requires research and thus resulting in higher cost. |
Future Expansion | Future expansion is very easy and simple. | Future expansion is most tedious and more costly. |
Safety and Responsibility | Single source of responsibility is there because the entire job is being done by one supplier. | Multiple responsibilities can result in question of who is responsible when the components do not fit in properly, insufficient material is supplied or parts fail to perform particularly at the supplier/contractor interface. |
Performance | All components have been specified and designed specially to act together as a system for maximum efficiency, precise fir and peak performance in the field. | Components are custom designed for a specific application on a specific job. Design and detailing errors are possible when assembling the diverse components into unique buildings. |
Pre-engineered steel building consist of the following:
- Primary framing (The main frames)
- Secondary framing (Z and C sections)
- Roof and wall panels (single skin and insulated sandwich panels)
- Structural subsystems (canopies, partitions, etc.)
- Floor systems (catwalks, platforms, etc.) and
- Other building accessories (sliding doors, roll up doors, windows, etc.)
Application for Pre Engineered Buildings
1. WAREHOUSES
2. FACTORIES
3. WORKSHOPS
4. OFFICES
5. GAS STATIONS
6. VEHICLE PARKING SHEDS
7. SHOWROOMS
8. AIRCRAFT HANGARS
9. METRO STATIONS
10. SCHOOLS
11. RECREATIONAL
12. INDOOR STADIUM ROOFS
13. OUTDOOR STADIUM CANOPIES
14. BRIDGES
15. RAILWAY PLATFORM SHELTERS
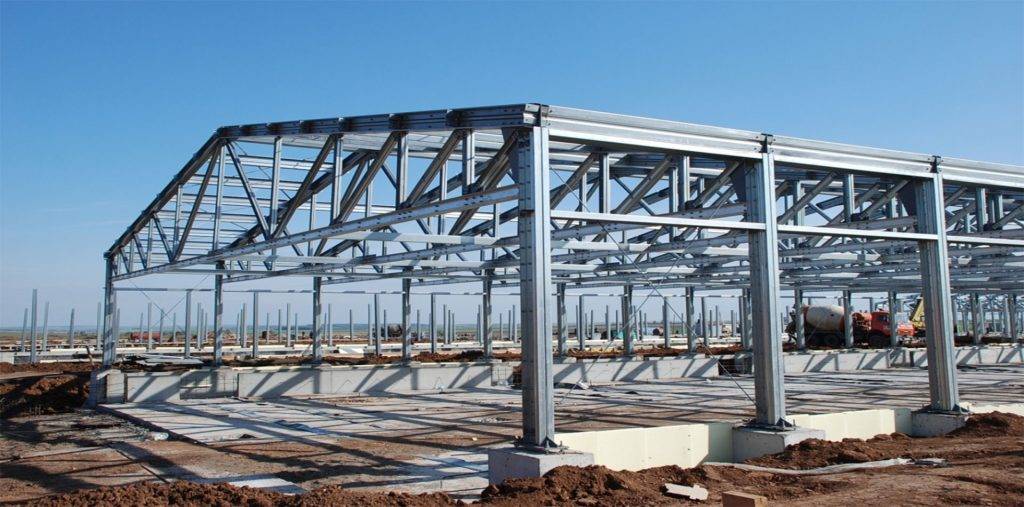


Pre Engineered Building
Lorem ipsum dolor sit amet, consectetur adipiscing elit. Ut elit tellus, luctus nec ullamcorper mattis, pulvinar dapibus leo.
WareHouse
Lorem ipsum dolor sit amet, consectetur adipiscing elit. Ut elit tellus, luctus nec ullamcorper mattis, pulvinar dapibus leo.
Multistore Building
Lorem ipsum dolor sit amet, consectetur adipiscing elit. Ut elit tellus, luctus nec ullamcorper mattis, pulvinar dapibus leo.
Advantages
- Construction time: PEB reduces the total construction cost by the least 40% which leads to faster occupancy and early revenue.
- Lower cost: Saving is accomplished in design, manufacturing and erection cost.
- Large clear span: In PEB the buildings can be given up to 90m clear spans which is the important advantage of PEB with column free space.
- Flexibility of expansion: PEB can be easily expanded in length by adding additional bays.
- Quality control: PEB’s are manufactured under controlled conditions depending on the site and hence the quality is assured.
- Low maintenance: PEB’s have high quality paint systems for cladding which gives long durability and low maintenance costs.